Keeping up with the latest advancements and trends in the ever-changing industrial industry is crucial for businesses to stay efficient and competitive. As technology advances, it brings with it new opportunities and challenges that are significantly altering the sector. Let’s examine the top five manufacturing trends for 2024.
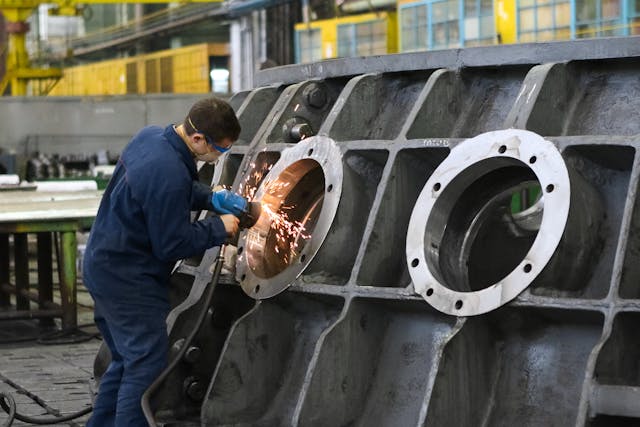
1. Supply Chain Resilience:
As a result of the need to reduce the risks associated with global disruptions like pandemics and geopolitical tensions, the manufacturing sector is placing a strong priority on supply chain resilience and localization in 2024. In order to avoid being overly dependent on a single source, this trend calls for diversifying one’s supplier base and implementing real-time supply chain analytics solutions, which allow for prompt reaction and predictive disruption management. The goal of localization initiatives is to lower logistical costs, improve supply chain dependability in the face of cross-border trade obstacles, and locate sourcing closer to manufacturing hubs or end markets. Achieving these objectives requires the use of digital technologies like blockchain, IoT, and AI, which provide safe transaction processes, effective tracking, and operational optimization through predictive analytics. The industry’s ability to more successfully manage future uncertainties is ensured by this change towards resilient, localized supply networks, which is a strategic drive towards more sustainable, efficient, and adaptive manufacturing processes.
2. Skilled Workforce Development:
The importance of skilled workforce development has grown in the era of automation, with a special emphasis on upskilling as a vital tactic to provide workers with the abilities they need to succeed in changing job roles. The need for a workforce skilled in these technologies and able to collaborate with cutting-edge systems is growing as companies embrace automation, artificial intelligence, and robots more and more. Upskilling programs aim to close the skills gap between workers’ present skill sets and the demands of the labor market of the future by making sure workers are not just competent with new technologies but also able to use them to improve quality, productivity, and innovation.
3. Smart Factory Evolution: Leveraging AI and IoT for Enhanced Productivity
Manufacturing is changing dramatically as a result of the Smart Factory movement, as businesses use AI and IoT technology more and more to increase productivity and operational efficiency. The integration of advanced systems that can communicate, analyze, and act upon data in real-time is at the core of this change, allowing firms to optimize production processes, minimize downtime, and quickly adjust to changing market needs. The contribution of laser equipment suppliers, who offer the necessary instruments for precision manufacturing and quality monitoring, is crucial to this technological advancement. These vendors, who provide state-of-the-art laser technologies that can be easily connected with AI and IoT systems for enhanced product customization, quicker production cycles, and less waste, are essential to the smart factory ecosystem.
4. Customization and Personalization:
A growing number of firms are implementing flexible production lines that can quickly adapt to shifting preferences and specifications in response to the growing needs of consumers for personalization and customization. This move towards flexibility enables businesses to cater to the specific needs of each client without sacrificing productivity or sharply raising expenses. Robotics, digital fabrication tools, and modular equipment are examples of advanced manufacturing technologies that enable production lines to be swiftly reconfigured for different goods or customized versions. Sophisticated software systems that enable real-time modifications and optimizations depending on incoming orders further help this adaptability.
5. Data Analytics and Artificial Intelligence (AI):
By the year 2024, the manufacturing sector is significantly capitalizing on the power of data analytics and artificial intelligence (AI) to revolutionize processes, enhance product quality, and foster innovation. Manufacturers are increasingly adopting AI-powered algorithms and machine learning models to analyze vast data sets, yielding actionable insights that inform predictive maintenance, streamline production schedules, and optimize operational efficiencies. In a market that is changing quickly, the strategic application of data analytics facilitates the implementation of data-driven plans, efficient risk mitigation, and the detection of emerging trends, all of which increase efficiency and strengthen competitive advantage.
Conclusion
The industrial sector will undergo a dramatic transformation in 2024, driven by data-based insights, sustainability programs, and technology breakthroughs. By embracing automation, digital twin technologies, sustainability practices, additive manufacturing, and data analytics, manufacturers may promote innovation, adapt to changing conditions, and prosper in a highly competitive global market.