In the intricate landscape of manufacturing, consistency is the linchpin of success. Process audits stand as the unsung heroes, safeguarding quality and efficiency. By meticulously examining various facets of production, they unearth potential pitfalls. Every cog in the manufacturing machine matters and audits ensure they’re operating optimally. Dive into ten common procedures that elevate the audit game.
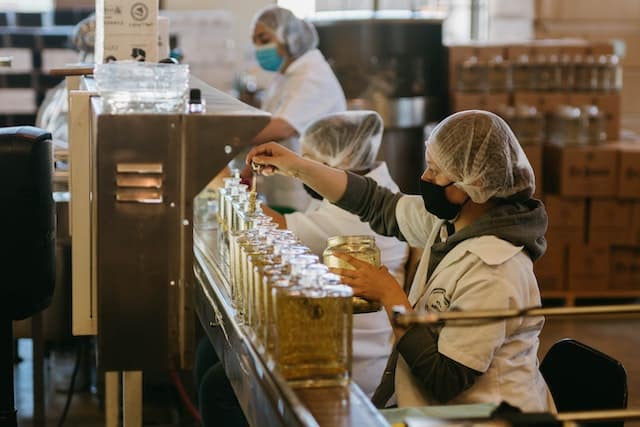
1. Documentation Review
At the heart of any manufacturing process lies a trove of essential documents. These records narrate the story of production, from inception to completion. A thorough review of these documents offers insight into compliance, consistency, and adherence to established standards. Discrepancies, if any, can highlight areas requiring immediate attention or improvement. Proper documentation is more than just paperwork; it’s the blueprint of manufacturing excellence.
2. On-site Inspection and Observations
While documents tell a tale, seeing the process firsthand paints the complete picture. On-site inspections provide a tangible feel of operations, ensuring that established protocols are being adhered to. It allows auditors to identify inefficiencies, risks, or deviations that might not be apparent on paper. Real-time observations can also gauge worker safety, equipment usage, and overall workflow dynamics. Such hands-on evaluations are foundational to comprehensive process audits, bridging the gap between theory and practice.
3. Employee Interviews
Employees, as the frontline operators, possess invaluable insights into the manufacturing process’s nuances. Engaging with them through interviews can uncover ground realities often missed in documented reviews. Their feedback can highlight procedural inefficiencies, shed light on safety concerns, or suggest potential improvements. Moreover, these interactions also assess if training and instructions are clearly understood and implemented. Tapping into this first-hand knowledge elevates the audit’s thoroughness, making it more holistic and actionable.
4. Process Mapping and Flow Analysis
Process mapping visualizes every step of the manufacturing journey, creating a clear, graphical representation of workflow. By analyzing this map, auditors can pinpoint bottlenecks, redundancies, or potential risks in the process. Flow analysis, on the other hand, dives deeper into resource allocation, timelines, and task interdependencies. Together, these tools offer a comprehensive view, facilitating more informed decision-making and optimization strategies. A well-analyzed process map is a beacon for continuous improvement and efficiency.
5. Validation of Measurement Tools
Precision in manufacturing hinges on the reliability of measurement tools. Validation ensures these tools provide accurate, consistent results over time. Without periodic validations, there’s a risk of producing off-spec products or wasting valuable resources. It’s not just about ensuring a tool’s functionality but its repeatability and reproducibility. Trusting the measuring tools translates to confidence in the final product, reinforcing the essence of quality assurance.
6. Review of Training Records and Competency Assessments
A well-trained workforce is the backbone of efficient manufacturing. Regularly reviewing training records ensures staff are equipped with up-to-date skills and knowledge. Beyond just training completion, competency assessments evaluate the effectiveness of these programs, gauging an employee’s true proficiency. These reviews pinpoint gaps in learning, suggesting areas for training enhancement or re-training. Such thorough evaluations fortify the production line, creating a seamless blend of skill and execution.
7. Sampling and Testing of Finished Products
Post-production scrutiny is as vital as monitoring the process itself. Sampling offers a snapshot of the entire batch, ensuring consistency and quality. Testing these samples, whether for durability, functionality, or compliance, affirms product reliability. Periodic testing, especially with random samples, can also forecast potential long-term issues or degradation. This proactive approach to quality not only builds trust but also sets a brand apart in competitive markets.
8. Efficiency and Waste Management Assessment
Optimal manufacturing strikes a balance between productivity and sustainability. Efficiency assessments monitor resource utilization, striving for the highest output with minimal input. Conversely, waste management evaluations target environmental impact, aiming to minimize emissions, scrap, and by-products. By refining these elements, manufacturers can achieve both economic and ecological harmony. Marrying efficiency with responsible waste management bolsters both profitability and environmental stewardship.
9. Review of Corrective and Preventive Actions (CAPA)
Manufacturing’s heart beats to the rhythm of continuous improvement. Rooted in this principle, CAPA addresses and prevents production hiccups. By leveraging standards like VDA 6.3, manufacturers can ensure robustness in their CAPA methodologies. Regular reviews validate the effectiveness of implemented actions and their adherence to quality benchmarks. Such rigorous practices identify, rectify, and inhibit recurring issues. Ensuring CAPA’s fidelity not only solidifies product quality but also drives industry-wide excellence
10. Verification of Supplier and Raw Material Quality
Quality manufacturing begins with superior raw materials. Ensuring supplier credibility is the initial step in this quality assurance journey. Rigorous audits of suppliers evaluate their processes, certifications, and compliance to set standards. Moreover, random sampling and testing of procured materials act as a further checkpoint. Emphasizing supplier and material quality not only guarantees superior end products but also nurtures long-term, trustworthy supplier relationships.
The Importance of Comprehensive Auditing in Manufacturing
Manufacturing isn’t just about producing; it’s about excellence in every step. Comprehensive audits shed light on hidden inefficiencies, ensuring quality remains paramount. With rigorous scrutiny, potential setbacks transform into stepping stones for improvement. The future of manufacturing leans on robust audit mechanisms, guaranteeing a legacy of precision and innovation. Every audit, therefore, is a commitment to unparalleled craftsmanship.