Manufacturers strive to improve their efficiency and production processes to perform well in a competitive business landscape. One strategy for this is providing high-level training programs for workers. Such training plays a critical role in enabling employees to develop the skills and knowledge needed to operate advanced machinery and implement new technologies allowing their companies to attain new heights.
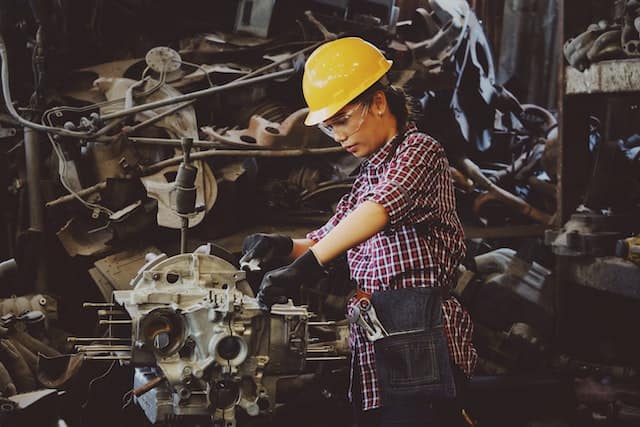
Types of High-Level Training
There are several types of high-level training programs that one can implement in the manufacturing industry. Some major types are discussed below:
Safety Training
Safety training is one of the most critical training courses in the manufacturing industry because it helps prevent accidents, injuries, and fatal incidents at your workplace. If you plan to provide this training, you can expect covering topics such as machine safety, hazard communication, and personal protective equipment (PPE) in a safety training program.
Technical Training
Technical training focuses on the technical skills required to operate machinery, equipment, and tools. If you want to implement technical training, you may teach your employees how to use overhead bridge cranes, set up machine programming, maintain technical equipment, repair machines, or take precision measurements under this program.
Quality Control Training
Quality control training is a type of high-level training program that you can use to teach employees how to ensure that the final product meets customer specifications and requirements. Such a program can include training in quality assurance procedures, inspection techniques, and statistical process control.
Lean Manufacturing Training
Lean manufacturing training is a methodology that aims to reduce waste and improve efficiency in production processes to make them more sustainable. It teaches employees how to identify and eliminate waste in all aspects of the manufacturing process, from raw materials to finished products. You should implement this type of training if you want employees to direct greater attention toward efficiency.
Soft Skills Training
Lastly, soft skills are non-technical skills that are vital for success in any industry, including manufacturing. Soft skills training can cover time management and problem-solving skills. You can introduce this training program if you want to make your team more cohesive and effective overall.
Benefits of High-Level Training in Manufacturing
Providing high-level training to employees in the manufacturing industry can be very fruitful. The major benefits are discussed below:
Increased Productivity
In the manufacturing industry, time is money, and any productivity improvement can translate to significant cost savings. With proper training, employees can learn how to use machinery and equipment more effectively, reducing production times and minimizing downtime due to equipment malfunctions.
Improved Quality Control
Quality control is critical in manufacturing to ensure that the final product meets customer specifications and requirements. By providing training on quality control procedures and techniques, employees will have lesser product recalls and returns. This means more satisfied customers.
Enhanced Safety
The manufacturing industry can be hazardous, with machinery and equipment that pose safety risks to employees. Providing safety training on topics such as lockout-tagout, personal protective equipment (PPE), and hazard communication can help to reduce accidents, injuries, and downtime, ensuring a safe working environment for all.
Reduced Costs
Training can help to reduce costs in several ways. By improving productivity and quality control, companies can reduce waste and rework, leading to lower production costs. Safety training can also help to reduce the costs associated with workers’ compensation claims and equipment damage.
Tips on Developing a High-Level Training Program
Now that you understand the benefits of high-level training programs, you may consider developing a training program for your employees. So, here are a few tips to help you plan effectively:
Conduct a Needs Analysis
Before designing a training program, it’s important to assess your employees’ current knowledge and skill levels. A needs analysis lets you understand the knowledge gaps in your team and decide which training you should initiate.
Set Clear Objectives
It is better to define the specific goals and objectives of your training program. This will help ensure that the training is focused and relevant to the needs of your employees and the company.
Incorporate Hands-On Learning
Manufacturing is a hands-on industry, and employees need to develop practical skills. Incorporate hands-on learning opportunities like equipment simulations or on-the-job training into your program.
Leverage Technology
Technology can help enhance training programs, such as virtual reality or augmented reality training simulations. Consider incorporating technology into your program to provide engaging and effective learning experiences.
Tailor Training to Job Roles
Lastly, you must be aware that every job role requires a different type of training. So, tailor your training programs to specific job roles and the skills required for those roles.
Conclusion
In conclusion, high-level training can take many forms, and it is a critical component of modern manufacturing operations because it has several benefits. So, you must invest in training programs that develop the skills and knowledge of your workforce to achieve long-term success in today’s fast-paced manufacturing environment.