Barrels and twin screws must work together in flooring plastic extrusion machines to optimize the polymer melt process, product quality, and energy efficiency. First, the barrel’s precise temperature control zones and twin screws’ design enable homogeneous plasticization and mixing.
Thus, extrudate molecular orientation and homogeneity are maintained. Manufacturers can lower material deterioration and energy usage through better screw geometry and barrel heating/cooling systems. This synergy permits the conversion of rigid PVC to TPO for ranged flooring specifications. So, carefully coordinating these components strengthens the mechanical qualities of flooring products and the plastic extrusion machine’s environmentally friendly operation.
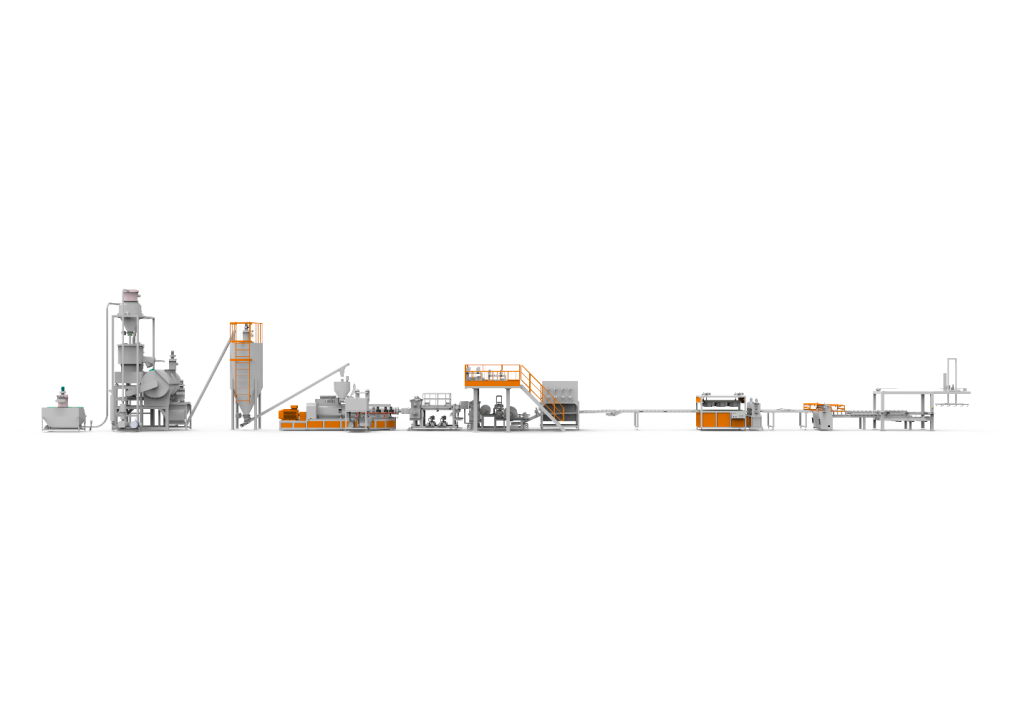
Flooring Plastic Extrusion Process
Here are the step-by-step flooring extrusion processes
- Raw material Preparation: This includes the careful selection of suitable plastic pellets, typically derived from thermoplastic resins like polyethylene, polypropylene, or polystyrene.
- Heating and Shaping: Subsequently, the raw materials are conveyed into a heating chamber, commonly referred to as an extruder. Within this apparatus, a rotating screw operates within a heated cylinder, facilitating the melting of the plastic pellets. This molten plastic is then propelled towards a die, where it adopts the desired shape or profile. The temperature and velocity of the screw are precisely controlled to ensure uniform heating of the plastic at the appropriate temperature.
- Extrusion: Through the die, the molten plastic is extruded to form various shapes and profiles, such as tubes, sheets, or pipes. The configuration of the die can be tailored to meet specific requirements. The extrusion process mandates strict regulation of temperature and pressure to ensure accurate shaping. Pressure levels within the extruder typically range from 1000 to 5000 psi, ensuring the plastic is propelled through the die with precision, maintaining the desired form.
- Cooling: Following extrusion, the plastic undergoes cooling procedures, utilizing methods such as water or air cooling. These techniques aid in solidifying the plastic, preserving its intended shape. The cooling phase plays a crucial role in determining the strength and durability of the final product.
- Cutting and Refinement: Once the plastic has sufficiently cooled and solidified, it undergoes cutting to attain the desired dimensions. Subsequent refinements may involve the removal of excess material, smoothing rough edges, or incorporating additional features like holes or grooves. The cutting and refinement process can be automated or carried out manually.
Flooring Plastic Extrusion Damage Causes
- Abrasive Wear from Fillers: Fillers in composite flooring materials cause abrasive wear, a problem for plastic extrusion machines. The fillers, including calcium carbonate and wood flour, may degrade the screw and barrel in the extruder. Consequently, it entails attentive material selection and recurrent upkeep to encompass its usefulness.
- Thermal Degradation: Polymer thermal deterioration may lower flooring quality under high temperatures. The plastic extrusion machine must have precise temperature control to avert decomposition, discoloration, decreased strength, and flooring material failure.
- Mechanical Stress and Misalignment: Mechanical stress from poor extruder setup or alignment may damage the screw and barrel. For example, unevenly loaded screws might wear or break, leading to lower machine productivity and flooring quality.
- Corrosion from Chemicals: Flooring additives and pigments may corrode plastic extrusion machine components. Critical components might be easily damaged due to corrosion. That risk may be lessened by using corrosion-resistant materials and thorough cleaning.
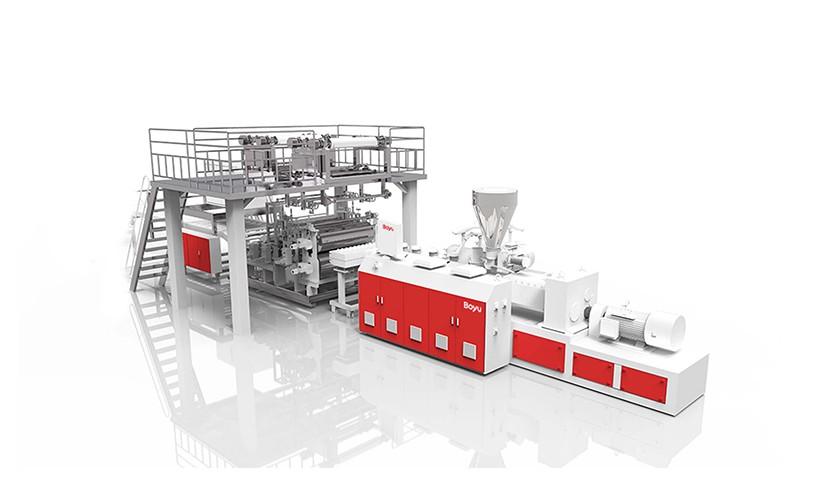
Restoration Guide for Both Barrels and Screws
The combined working quality of the screw and barrel components has a significant impact on the plasticization of materials, the quality of products, and production efficiency. Their working quality is related to the manufacturing accuracy and assembly clearance of the two components. When severe wear occurs and the output of the extruder decreases, maintenance or replacement of the screw and barrel should be arranged.
Restoration Techniques for Extruder Screws
Depending on wear and extrusion process requirements, numerous methods restore screws in plastic extrusion machines. Thermal spraying with wear-resistant metals rebuilds screw diameter and profile while abating barrel clearance. Weld overlaying using carbide-rich materials (C, Cr, Vi, Co, W, and B) might enhance screw wear and corrosion resistance. Flooring manufacturers benefit when processing abrasive or corrosive materials. Finally, potent chromium plating is cost-effective for screws under less severe working situations despite its tendency to delaminate.
Advanced Repair Methods for Extruder Barrels
Precision machining and alloy re-casting or nitrided alloy steel bushings are extruder barrel repair technologies. Direct boring and grinding of the worn barrel to a new diameter and screw manufacturing may restore operating clearance between the screw and barrel. A nitrided alloy steel bushing restores performance in worn barrels in high-stress feed and homogenizing sections.
Considerations for Restoration vs. Replacement
A thorough study beyond cost comparison defines whether to restore or replace damaged plastic extrusion machine components. The choice should weigh restored components’ life and performance against new ones. Thermal spraying and weld topping may improve the serving time of a screw. However, in abrasive situations, a new screw may last longer. Similarly, boring and re-nitriding a barrel should evaluate its functional advantage against the dependability of a new barrel.
Material Selection for Durability Enhancement
Screws and barrels for flooring plastic extrusion machines must be made of suitable materials to endure. For processing flooring materials with abrasive additives, nitriding or bimetallic lining boosts wear and corrosion resistance in 38CrMoAlA and 40Cr. To balance cost and function, the material and treatment techniques should match the wear issues of the extruded flooring materials.
Conclusion
Boyu is among the veteran twin screw extruder manufacturers that create cutting-edge SPC and LVT flooring production lines. They provide CE-certified PET/PP, WPC/PVC foam board, and PVC imitation marble sheet lines. Their environmentally friendly, durable, and waterproof equipment has over 90 technological patents and a solid R&D base. Boyu’s plastic extrusion technology is safe, simple to use, and produces high-quality results for worldwide customers.
Visit Boyu’s website for more details.