Efficiency and quality are crucial in the fiercely competitive corporate sector. Businesses must utilize efficient production procedures to meet customer needs and have a competitive edge while producing large commercial parts. Compression molding is one such method that has grown in popularity. The production of large commercial parts will be covered in detail in this article. This tutorial will offer helpful insights into large-scale part production, from comprehending the process to selecting the appropriate materials and locating the best manufacturer.
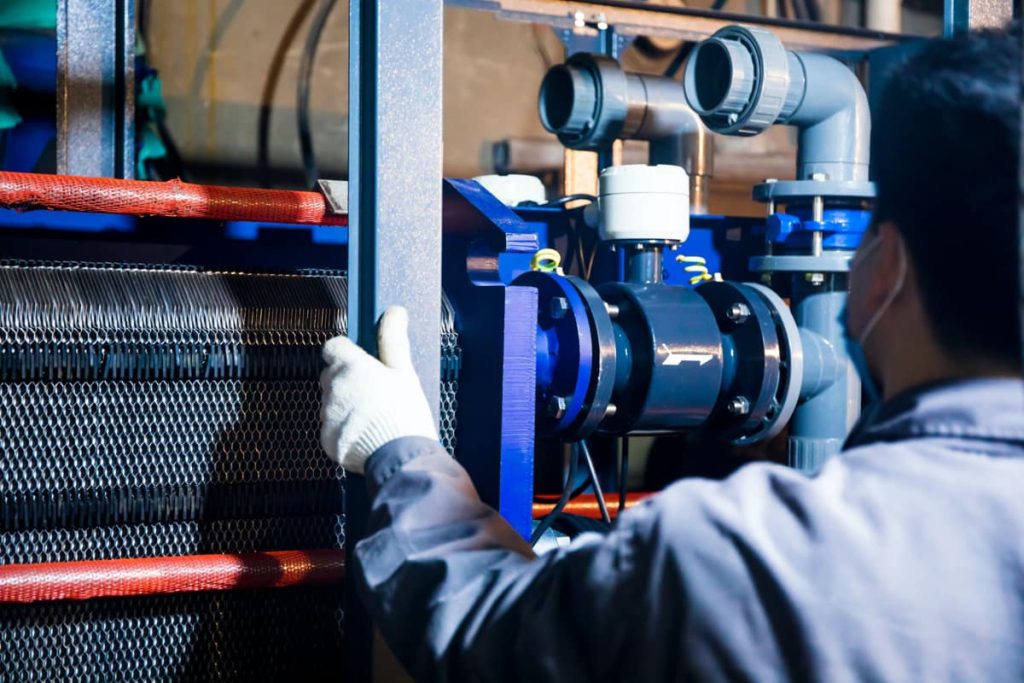
- Understanding the Compression Molding Process
Compression molding is a flexible manufacturing technique that compresses and shapes raw materials under intense pressure and heat to produce huge commercial items. This method is frequently used because it can consistently produce delicate details and complex geometry. Preparing the raw ingredients, which are frequently in the form of pellets, powders, or preforms, is the first step in the procedure. These materials are put into a heated mold cavity to guarantee proper material flow and distribution. Next, pressure is applied. The mold is opened, and the finished portion is removed as the substance cools and solidifies.
- Choosing the Right Materials
In order to produce large commercial parts, it is crucial to choose the right materials. It is necessary to consider aspects like mechanical qualities, sturdiness, chemical resistance, and affordability. Thermoplastics, thermosetting plastics, and composites are only some materials that can be employed in compression molding. Thermoplastics are frequently utilized in applications where impact resistance is essential because of their strength and flexibility. On the other hand, thermosetting polymers provide exceptional dimensional stability and heat resistance, making them perfect for parts exposed to high temperatures. Composites offer improved strength and lightweight features by combining the capabilities of many materials. You can work with compression molding companies to select the best materials for your production needs by communicating with them about the specific needs of your company and the intended use of the parts.
- Finding the Right Compression Molding Service Provider
Choosing the appropriate compression molding service provider to work with might make all the difference when making huge commercial products. With so many possibilities on the market, it is important to consider several variables before choosing. Start by evaluating the company’s production of large component’s experience and skills. Seek out a company with a history of completed projects and happy customers. A business with substantial compression molding expertise will have the knowledge and abilities to overcome unforeseen obstacles and produce high-quality products. Additionally, confirm if the business has cutting-edge facilities and equipment to efficiently handle large-scale production. Competent personnel, access to cutting-edge molding machinery, and quality control procedures are all part of this. Moreover, consider the business’s capacity to deliver unique solutions suited to your particular needs. In order to ensure successful cooperation with the compression molding company, effective communication, quick reaction times, and a collaborative attitude are essential.
- Quality Control and Assurance
In order to produce large commercial parts that match industry standards and customer expectations, strict quality control procedures must be maintained. To guarantee constant part quality throughout the production cycle, the compression molding service provider should have strong quality control procedures in place. This entails checking the quality of the raw materials, keeping track of the process variables, and thoroughly inspecting the end products. Failure mode and effects analysis and statistical process control are two quality assurance approaches that can be used to proactively identify and handle any possible problems.
Implementing a comprehensive quality management system based on the ISO 9001 standard is an even better alternative as it takes a more holistic approach than isolated quality assurance approaches. Performing regular internal ISO 9001 audits ensures not only compliance with the standard but also effective quality processes covering all processes necessary in the production of large commercial parts.
In addition, maintaining openness and ensuring that everyone is on the same page about quality expectations will require regular contact with the compression molding company regarding quality standards and inspection procedures.
- Timely Production and Delivery
To achieve project timelines and customer expectations, timely manufacturing and delivery of big commercial parts are essential. Discuss production schedules and gauge the service providers capacity to satisfy your needs before committing to the relationship. Consider elements including the company’s track record of timely completion, lead times, and production capacity. Effective project management, efficient logistics, and clear communication are crucial to ensure flawless collaboration between your company and the compression molding service provider. Your parts’ timely completion and delivery can be ensured by providing regular status updates, milestone reviews, and proactive problem-solving.
Conclusion
It takes careful planning and cooperation with reputable compression molding service providers to produce huge commercial parts for your company. You can achieve productive and economical production by comprehending the compression molding procedure, choosing the appropriate materials, and locating the best manufacturer. To produce high-quality parts that satisfy industry standards, collaboration in design and engineering, the implementation of strict quality control procedures, and timely production and delivery are crucial elements. By following this thorough manual, your company can successfully meet client requests while navigating the world of large-scale part production.