Product quality is crucial since it influences a company’s performance and contributes to building its reputation in target markets. The ability of businesses to produce high-quality goods that continue to satisfy client needs may result in lower production costs, greater investment returns, and higher revenue.
Therefore, let’s now explore five keys to achieving this.
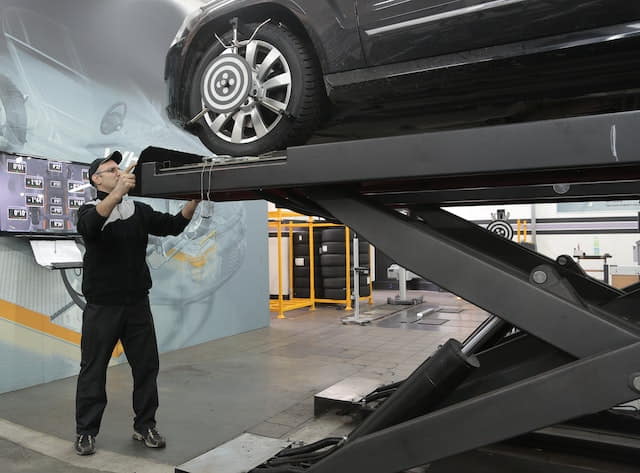
Design and Development of Products Should Come First
Quality starts with product development and design since consumer expectations determine quality. How closely does the design of your product fit what the intended buyer is seeking?
Sometimes businesses encounter quality problems and erroneously believe the manufacturer is to blame. When you look closer, you discover the issue with how the corporation created the product. No matter how expertly a product is manufactured at the factory, if the design is incorrect from the start, it won’t matter.
The APQP methodology may define the quality standards that will allow you as a provider to create a product that pleases your client. To satisfy customer requests, you must ensure that the materials, dimensions, components, and all other pertinent elements are optimized.
Testing of Products and Markets
Before launch, it is crucial to evaluate and test your product. You’ll likely need to correct bugs, add features, and change functions, so the product satisfies user wants and demands. Beta testing of the product is required, as is market research to see how customers would respond to it.
You may compare the performance of your product in a controlled setting and the actual world by doing product testing. You will test your product’s support, marketing, and usage to gauge client approval and adjust the product’s quality appropriately.
Define the Meaning of Quality for Your Brand
If you have created a product that can satisfy consumer demands, you must provide the manufacturer with your specs. To effectively keep your manufacturer responsible to them, these specs should be as explicit as feasible. It would help if you also put your quality control procedures into practice, such as product quality checks.
During these inspections, you’ll also remove manufacturing units to see how well they correspond to your specs. However, to add detail, you must establish your AQL levels, which are based on the acceptability quality level approach. In other words, you must categorize the many potential flaws and choose the proportion of permitted flaws.
Integrate Quality Into Your Company’s Culture
Although putting a Quality Management System in place is crucial, seeming to complain is insufficient. Your whole company has to be strongly rooted in these quality concepts. When it comes to what makes an excellent product, the whole team must be in agreement.
It is a high-tech solution for some while being a low-cost offering for others. Regardless of your choice, ensure your supervisors keep hammering home the point. You can convince everyone to support your idea of quality by doing this.
Management must allow workers to participate in the development process to produce items that meet your quality standards. Employees won’t need to provide you with any input if they don’t feel like they have a voice in the project. Additionally, it would be best to have this input since your staff members directly impact productivity. Allow staff members to discuss deviations from the product plan or quality standards openly.
You must provide just the proper direction to your personnel during the product development process. They will stop being creative if you supervise them excessively. They won’t be certain of their ability to make independent judgments if you are overly lenient. Allow your staff to watch the operational procedures and set up sessions where they may make suggestions for changes.
Implement a System for Quality Management (QMS)
It is simply a collection of internal regulations your business creates and then adheres to assure the products’ quality. Putting in place a QMS may help you maintain compliance with laws and industry standards while ensuring the best possible goods.
To set up a quality management system, you must go through many steps known as Design, Build, Deploy, Control, Measure, Review, and Improve.
Conclusion
What quality is, many professionals have varied viewpoints. Don’t forget to develop a plan, implement a quality management system, instill quality into the company culture, and conduct frequent product and market testing. All of this puts you on the right track to producing items of the highest quality that will thrill your clients and ensure that they return for more.