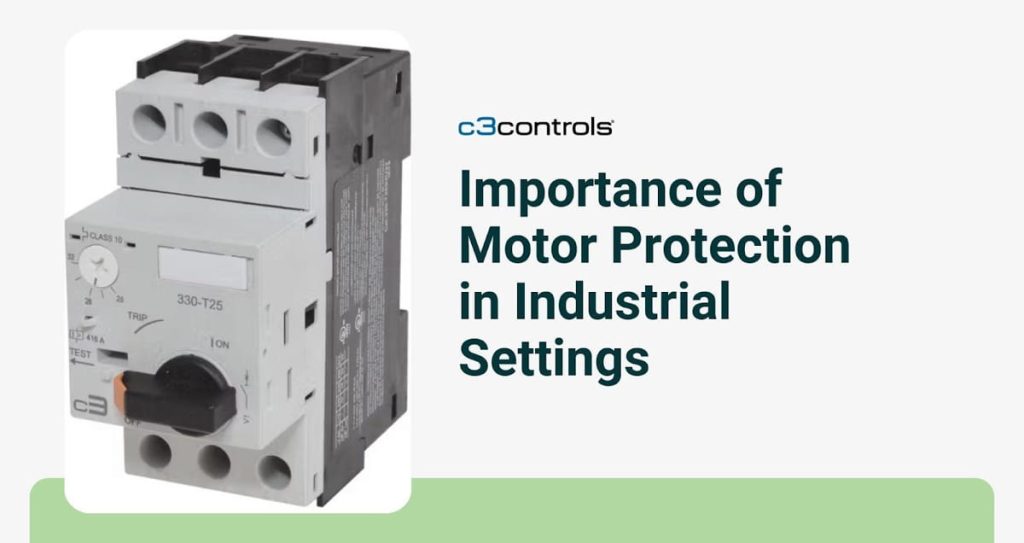
Industrial settings rely heavily on motors to power machinery, equipment, and production processes. Motors drive everything from conveyor belts and pumps to fans and compressors. However, the continuous operation of motors in high-demand environments exposes them to risks like overheating, electrical faults, and wear. Protecting these motors becomes essential to prevent downtime, maintain safety, and avoid costly repairs.
In this blog, we’ll discuss why motor protection is crucial, the types of protection systems available, and the significant benefits of implementing motor protection in industrial environments.
Why is Motor Protection Important?
Motor protection is a system of devices, controls, and procedures that guards motors from damaging conditions, such as electrical overloads, mechanical failures, and environmental factors. Without protection, motors may fail unexpectedly, leading to production stops, equipment damage, and safety hazards. Motor protection ensures that motors run efficiently and safely, extending their lifespan and improving overall plant performance.
Let’s explore some of the main risks motors face and why motor protection is essential:
- Overloading: Motors often work under high loads in industrial applications, which can lead to excessive current draw. Overloading not only strains the motor but also increases its temperature, eventually causing insulation damage and other failures.
- Overheating: Excessive temperatures damage motor windings, shorten motor life, and can cause a motor to fail entirely. Motors heat up due to heavy loads, poor ventilation, or operation in hot environments, and proper motor protection can detect and respond to high temperatures.
- Short Circuits and Electrical Faults: Electrical faults, such as short circuits, send large currents through the motor, which can damage it instantly. These faults may arise from faulty insulation, wiring problems, or other electrical issues. Protection systems can detect such faults and shut down the motor to prevent damage.
- Voltage Imbalance: When the supply voltage is unbalanced, the motor may face uneven current distribution in its windings, which leads to overheating and eventual failure. Voltage imbalances can come from various sources, including issues with power supply and faulty wiring.
- Environmental Factors: Industrial environments may expose motors to dust, chemicals, and moisture, which can damage sensitive parts over time. Motor protection includes enclosures and environmental safeguards to keep motors safe from harmful conditions.
Motor protection safeguards motors from these issues, enabling them to operate without interruption and minimizing risks to workers and equipment.
Types of Motor Protection in Industrial Settings
Industries use different motor protection systems depending on the specific needs and risks associated with their motors. Here are some commonly used types of motor protection:
- Overload Protection
Overload protection devices monitor the current flowing through the motor. When the motor experiences an overload condition, these devices detect the excess current and disconnect the motor from the power supply. Common overload protection devices include:- Thermal Overload Relays: These relays contain a bimetallic strip that bends when it heats up under high current. When the strip bends, it trips the relay, cutting off the power to the motor.
- Electronic Overload Relays: These devices use electronic sensors to detect overload conditions. They are more accurate and can respond faster than thermal relays, making them suitable for high-precision applications.
- Short Circuit Protection
Short circuits can cause severe damage to motors and create safety hazards. Fuses and circuit breakers provide short circuit protection by breaking the circuit if a fault occurs, cutting off the power to the motor. Circuit breakers are especially common in industrial settings because they can reset and provide continuous protection. - Ground Fault Protection
Ground faults occur when electrical currents flow through an unintended path, which may damage the motor and pose risks to workers. Ground fault protection devices detect these currents and disconnect the motor from the power source. In some industries, ground fault relays or specialized protection devices are mandatory to prevent serious incidents. - Temperature Protection
Motors operating in demanding environments or under heavy loads can overheat. Temperature protection devices monitor the motor’s internal temperature and activate a shutdown if it reaches unsafe levels. This type of protection includes:- Thermistors: Small temperature sensors placed within the motor windings to monitor internal temperature.
- Thermostats: Devices that cut off power when the motor exceeds a certain temperature.
- Phase Failure and Voltage Imbalance Protection
Motors running on three-phase power can suffer from phase failure or voltage imbalance. These conditions result in uneven current distribution, leading to excessive heating and potentially damaging the motor. Protection devices detect any phase imbalance or failure and disconnect the motor to prevent harm. - Environmental Protection
In environments with dust, moisture, or chemicals, protective enclosures, seals, and coatings protect motors from damage. These measures keep contaminants away from sensitive motor parts, ensuring safe and reliable operation.
Benefits of Motor Protection in Industrial Settings
Implementing motor protection brings numerous benefits to industrial facilities. Here are some key advantages:
- Increased Motor Lifespan: Motors are expensive, so extending their life is financially beneficial. Motor protection systems detect harmful conditions before they cause irreversible damage, ensuring motors operate safely and efficiently.
- Reduced Downtime: Unexpected motor failures lead to costly downtime, affecting production schedules and delivery times. By preventing issues like overloads and electrical faults, motor protection reduces the likelihood of breakdowns, keeping operations running smoothly.
- Improved Safety: Faulty motors pose risks to workers and equipment. Ground fault protection and other motor safety devices reduce the chance of accidents, creating a safer work environment for employees.
- Energy Efficiency: A motor operating under normal, well-monitored conditions uses energy more efficiently. Protection systems prevent overheating, overloading, and voltage issues, helping motors run at optimal efficiency and reducing energy consumption.
- Cost Savings: Repairs and replacements for damaged motors are costly, as are the associated labor and downtime. Motor protection helps avoid these expenses by identifying issues early, reducing maintenance costs, and protecting investments.
- Compliance with Regulations: Many industries have safety regulations that require motor protection to prevent hazards and ensure workplace safety. Implementing motor protection helps businesses stay compliant with these standards, avoiding potential fines or legal issues.
Implementing Effective Motor Protection
To set up effective motor protection, industries must assess their specific needs. Here are some tips for implementing robust motor protection systems:
- Analyze Motor Requirements: Identify the power, voltage, and environmental requirements for each motor. This will help determine the appropriate protection devices needed.
- Choose Reliable Devices: Invest in high-quality protection devices that suit the environment and application. For example, electronic overload relays may be more suitable for complex automation systems, while thermal overload relays may be effective for simpler setups.
- Monitor and Maintain: Motor protection devices require periodic testing and maintenance. Regular checks help ensure they perform accurately and reliably, providing the best protection.
- Automate Where Possible: Automated motor protection systems, controlled by sensors and programmed logic controllers (PLCs), provide seamless monitoring and response, especially in environments that require constant monitoring.
Motor protection is essential in industrial settings to keep motors operating safely and efficiently. It reduces risks, protects valuable equipment, and ensures consistent production. As industrial environments become more demanding, investing in comprehensive motor protection systems will pay off in terms of safety, efficiency, and cost savings.