Since the beginning of the year 2020, companies of all scales (local, national, regional, and global) have encountered unprecedented challenges. Manufacturing in every sector is experiencing a skills gap, and machine shops are no different. Shops of all sizes have adjusted their strategies to compete better. The largest obstacles facing machine shops are universal despite differences in focus between large and small businesses.
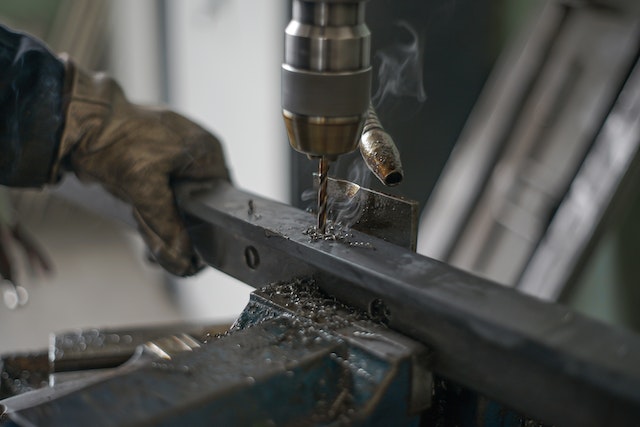
Customization and Inventory
Customers desire more individualized service even as they demand quicker shipping times. Manufacturers seek to match the wants of their clients, which involves offering additional possibilities for customized parts. In turn, the engineering division provides cost estimates based on these labor needs. Fortunately, more options for individualized components and goods are made possible through turnkey ERP solutions, designed to combat the many unique challenges machine shops face.
The issue of inventory management is complicated because shops trying to take advantage of price drops in supplies may find themselves with an excess of materials they can no longer use due to the high degree of customization. To make educated decisions about inventory management, product cycles, and shipping schedules, stores should collect and analyze as much data as possible.
Competition and Scheduling
Customers, it would appear, want goods immediately. Clients not only put time pressure on factories to create parts, but they also frequently make changes to requirements and even seek special attention in emergencies. The business will increase for stores that can shift gears and adapt rapidly, but owners will have more on their plates.
Speed
Production and delivery time are also significant obstacles for the metal fabricating sector. Customers still expect the exact rapid production turnaround times that existed before the epidemic, even though they are aware of the difficulties in the distribution network and the rising costs. They want immediate fulfillment of their obligations. Retailers that can fulfill their customers’ aggressive deadlines will thrive, whereas those who can’t go out of business.
Staffing
Although this argument has been made many times before, that does not make the underlying issue any less severe. In the face of the retirement of experienced operators, it is challenging to train replacements. Starting has an advantage because younger generations are more comfortable with computers and can quickly pick up machine shop operations.
Nonetheless, the metalworking sector is looking to form novel collaborations with local colleges and employment training programs to train better and recruit new operators. You cannot expect to learn how to use an electric press brake properly without proper instruction.
Therefore, the industry needs to look for novel approaches and collaborative efforts to train the personnel who will run metalworking machinery and oversee quality control.
New Skillsets and Automation
The standard for shaping and designing precision metal components has been raised with the advent of computer numerical control (CNC) equipment. Robots are increasingly able to take over several previously human-only tasks. Familiarity with numbers and code is necessary for operating a CNC machine.
Operators of such precision equipment must be familiar with the materials and components they can use. Quality standards for precision components should be as stringent, and requirements can be stated in millimeters.
The thickness, malleability, and hardness of the metal all play a role. More highly skilled workers are needed to operate these new devices, and locating them may be challenging and expensive.
Diversification
The processing of metals is a multi-step procedure. Forging, stamping, drilling, cutting, and bending transform sheet metal and other inputs into the desired forms. These tasks call for specialized tools and expertise. They also lead to defective pieces with “burrs,” a term for surface roughness.
CNC machining and other thermal procedures can leave behind tiny shards of re-hardened molten metal. The typical business practice involves shipping off parts for finishing and deburring by third parties; however, convenient one-stop shops exist.
Thus, a competitive advantage may be gained by increased production speed. Machines with computerized finishing and deburring capabilities allow machine shops to integrate finishing in-house and regain control of their production schedule and quality.
Maintenance
Naturally, there are fresh worries about the upkeep of every cutting-edge machine. An operator may be proficient in programming but unlikely to be adept in keeping the machine in working order.
The shop’s proprietors must carefully consider the longevity, user-friendliness, and maintainability of any machinery added to a machine shop to overcome a prevalent problem.
Bottom Line
Technology in metalworking has allowed for significant advancements since the days of hand-forming and hand-filing components. Machine shops can perform the task by implementing technology upgrades and personnel training for much more complicated and automated procedures.